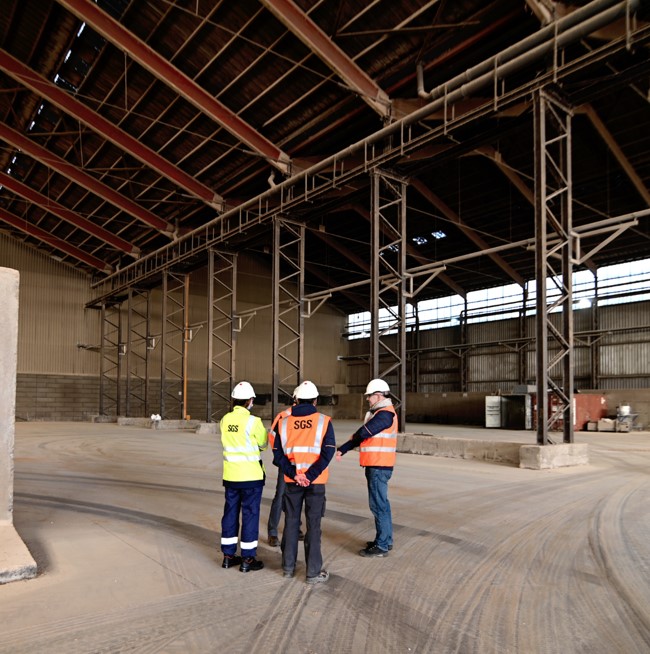
Why Toowoomba?
Toowoomba, a fast-growing industrial hub, selected for its proximity to established Agricultural, Civil, Resource sectors and future support of the Australian Defence Force. This location strengthens Redback’s position in Queensland and beyond, offering clients bespoke solutions that meet their unique requirements.
Workshop Setup for Premium Service
Spanning 1950m³ of covered space, our Toowoomba workshop is built for growth and currently equipped to deliver a wide range of services including:
Premium Drilling Thread Repairs: Ensuring that your tubulars remain in optimal condition with expert repairs to your premium threaded connections.
Custom Manufacturing and Precision Machining: Providing precise manufacturing and machining solutions for custom components and tools, designed to meet the unique needs of your operations.
Dedicated Industry Support: Offering comprehensive services to the Resources, Civil, and Agricultural sectors, we are committed to enhancing the efficiency and performance of local industries.
Our Toowoomba workshop enables us to reduce downtime for clients, maximise operational efficiency, and deliver solutions that ensure long-term success. Whether it’s precision repairs or custom manufacturing, we are committed to meeting the unique demands of each project with unmatched quality and precision.
A Future Built on Strong Partnerships
As we look to the future, we are excited about the possibilities this new workshop brings.
The Toowoomba facility plays a crucial role in fulfilling that mission, and we look forward to partnering with industry leaders to drive success and innovation across multiple industries.
The Toowoomba team specialises in crafting innovative, bespoke solutions that directly address the challenges faced by our clients. With a commitment to providing reliable and flexible support, we continue to strengthen our reputation for engineering excellence. As we grow, we are focused on expanding our capacity and capabilities to meet the evolving needs of our clients and the industries we serve.
Celebrating Our Opening
We’re thrilled to invite clients, industry partners, and community members to join us for an opening day event at the Toowoomba workshop, where we’ll showcase our new facility and capabilities. Further event details will be announced soon.
For more information about the Toowoomba workshop and to explore our custom solutions, please contact us directly.
Clint Russell
Redback Drilling Tools and Manufacturing
Business Manager
t: +61 1300 781 744